Механические и электрические вибрационные испытания подшипников
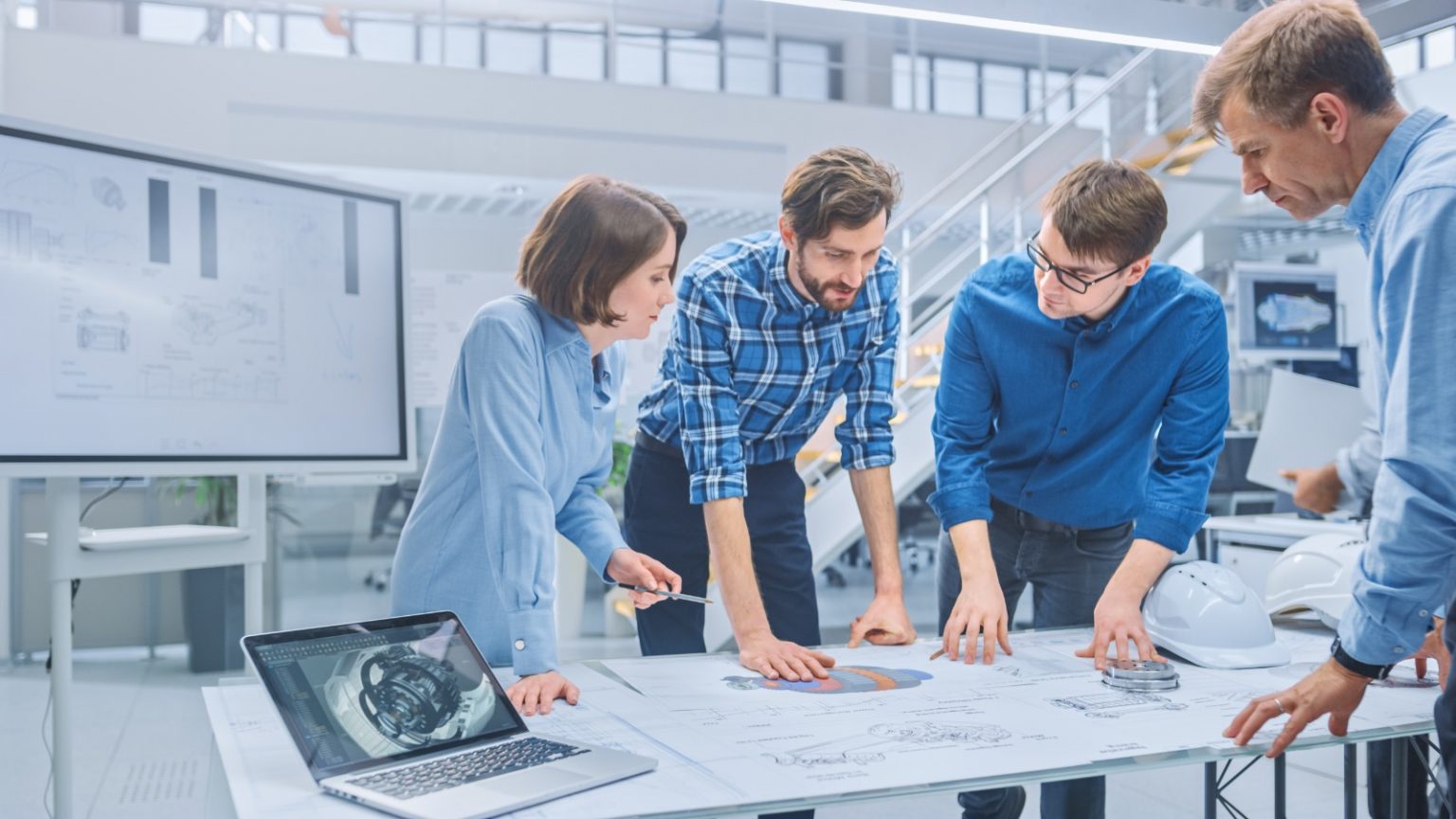
ПРЕДИСЛОВИЕ
Большинство вращающегося оборудования зависит от подшипников с качающимися элементами для успешной работы. Функционально подшипники с качающимися элементами несут нагрузку вала, внутренне позиционируют вал и разделяют вращающиеся и неподвижные компоненты.
Выявление неисправностей в подшипниках с качающимися элементами до того, как они нарушат работу или повлияют на качество продукции, является основой большинства программ предиктивного обслуживания. Путем проведения обзоров и оценки результатов работы оборудования на регулярных интервалах пытаются выявить неисправности подшипников до того, как они станут катастрофическими.
В течение многих лет эти обзоры обычно проводились очень надежно с помощью механического анализа вибрации (MVA). В настоящее время существует несколько методов для выявления неисправностей в подшипниках с качающимися элементами. В этой статье будет предпринята попытка идентифицировать эти методы от механического анализа вибрации до анализа электрической сигнатуры (ESA).
ВВЕДЕНИЕ
В данной статье описываются 4 стадии отказа, которые проходят большинство подшипников с качающимися элементами в процессе типичного усталостного отказа. Также рассматривается использование анализа вибрации, оболочечного сигнала, ультразвукового обнаружения и анализа электрической сигнатуры для выявления стадий отказа подшипников с качающимися элементами.
Из-за относительно низкой стоимости и высокой надежности подшипников с качающимися элементами они чаще всего используются в промышленности. Однако из-за близких зазоров и очень высокополированных поверхностей неисправности подшипников все же возникают. Их устранение практически всегда означает полную замену неисправных подшипников.
Производители подшипников предоставляют очень подробные процедуры по обслуживанию, смазке и эксплуатации для максимизации срока службы этих очень важных машинных компонентов. Долгий срок службы подшипников может быть достигнут путем соблюдения этих практик. Кроме того, практика "Точного обслуживания" доказала, что возможно продлить срок службы подшипников в 5-10 раз дольше, чем это было ранее, с минимальными дополнительными усилиями.
Однако из-за рабочей среды, непроизводственных толерантностей, ошибок в сборке или даже работы самого оборудования эти подшипники могут выходить из строя. Если неисправности обнаруживаются до полного отказа, то последующий ущерб и ремонт обычно ограничиваются заменой самого подшипника.
Итоговым результатом является отказ из-за усталости одного или нескольких основных компонентов подшипника.
ПРИЧИНЫ ОТКАЗА ПОДШИПНИКА
Большой производитель подшипников оценивает, что около 16% отказов подшипников являются результатом неправильного обращения с ними. Это вызвано неправильным хранением, транспортировкой или установкой подшипников. Оставшиеся 84% подшипников с качающимися элементами устанавливаются без дефектов. На этой стадии нет признаков неисправностей подшипников. Если при исходной эксплуатации подшипника есть признак неисправности, то это обычно проблема с посадкой подшипника или сборкой.
36% отказов подшипников с качающимися элементами являются результатом недостаточной смазки, пересмазки, недосмазывания, неправильного смазочного материала, смешивания смазок или слишком тонкого слоя смазки, часто вызванных избыточным движением вала (вибрацией).
34% замен подшипников с качающимися элементами производятся из-за операционных факторов, дисбаланса, неправильного выравнивания или, в некоторых случаях, из-за замены подшипников по другим требованиям обслуживания, таким как программы профилактического обслуживания.
Последние 14% отказов происходят из-за загрязнения.
ЗАМЕНА ПОДШИПНИКА
Основной вопрос, связанный с отказом подшипника с качающимися элементами, - "Когда следует заменить подшипник?"
Это может быть определено только заводом. Влияет ли отказ на качество продукции? Влияет ли он на работу предприятия? Какова доступность заменяющего подшипника? Для более точной оценки состояния подшипника и определения оптимального времени его замены важно понимать стадии отказа подшипника.
СТАДИИ ОТКАЗА ПОДШИПНИКА
Для более глубокого понимания отказа подшипника важно знать, что большой производитель подшипников провел исследования для определения того, как подшипники с качающимися элементами отказывают. Их исследование показало, что подшипники с качающимися элементами функционируют примерно 80% своего полезного срока службы без дефектов. Когда отказ все-таки происходит, обычно можно выделить 4 характерные фазы отказа.
Стадия 1: Отказы подшипников с качающимися элементами обычно начинаются под поверхностью. Обычно они начинаются с глубиной в 0,1-0,125 мм под поверхностью канавки. На этой стадии оценивается, что осталось 10-20% срока службы подшипника.
Стадия 2: По мере ухудшения дефекта на поверхности возникают микроскопические ямки (<40 микрон) на поверхности дефектного компонента. Это считается стадией 2, и оценивается, что остается от 5 до 10% срока службы подшипника.
Стадия 3: Дальнейшее ухудшение приводит к началу обломов, трещин и/или отколов, которые обычно связаны с отказами подшипников с качающимися элементами. Остается от 1 до 5% срока службы подшипника.
Стадия 4: Когда возникают множественные трещины, избыточные обломы или отколы, это четвертая и последняя стадия отказа подшипника. Зачастую качающиеся элементы начинают деформироваться, а клетка может распадаться или ломаться. Остается от 1% до 1 оборота срока службы подшипника.
Большинство технического персонала предпочитает заменять подшипник на стадии 3. Дефект визуально виден, но повреждение все еще ограничено только подшипником. На стадии 1 практически невозможно определить дефект, так как он находится под поверхностью. На стадии 2 дефекты невидимы невооруженным глазом и требуют увеличительного стекла или даже микроскопа для определения дефекта.
Если подшипник достигает стадии 4, то машину следует немедленно вывести из эксплуатации и заменить подшипник. Продолжение работы машины в конечном итоге приведет к полному отказу подшипника. Такой вид отказа снимет машину с эксплуатации и обычно вызовет избыточные повреждения машины.
ПОЧЕМУ НЕОБХОДИМА ПРЕДИКТИВНАЯ ТЕХНИЧЕСКАЯ ЭКСПЛУАТАЦИЯ ДЛЯ ОТКАЗОВ ПОДШИПНИКОВ С КАЧАЮЩИМИСЯ ЭЛЕМЕНТАМИ
Программы предиктивного технического обслуживания основаны на исследованиях, которые определили, что 89% отказов имеют случайный характер, и 68% из них происходят непосредственно после установки или ремонта. В общем, это означает, что вероятность отказа фактически увеличивается при проведении регулярных инспекций и работ по профилактическому обслуживанию.
Эффективная программа предиктивного технического обслуживания использует рабочее состояние машины для определения необходимости технического обслуживания. Самые эффективные программы признают 3 фазы предиктивного технического обслуживания: обнаружение, анализ и коррекция.
Фаза обнаружения: Фаза обнаружения является самой важной, поскольку она используется для выявления отказов оборудования. Эффективная программа предиктивного технического обслуживания будет выявлять такие отказы за достаточно продолжительное время до того, как произойдет сам отказ подшипника, и позволит выполнить ремонт или замену подшипника до отказа. Философия фазы обнаружения заключается в том, чтобы провести быстрый обзор как можно большего количества машин. Фаза обнаружения выявляет потенциальные отказы подшипников. Чем быстрее можно провести эти обзоры, тем больше машин можно проверить, что приводит к более эффективной программе.
Примечание: Большинство зрелых программ предиктивного технического обслуживания выявляют 1-2% новых проблем при каждом обзоре. Это означает, что если проверить 300 машин, то будет выявлено всего 3-6 новых проблем.
Фаза анализа: Фаза анализа может потребовать дополнительного тестирования или даже дополнительной технологии для определения степени и причины отказа. Обычно это самая затратная часть программы предиктивного технического обслуживания по времени. Если во время фазы обнаружения было взято достаточно данных для точного анализа, это затратит много времени на фазу обнаружения. Это снизит количество машин, способных к проверке, или увеличит необходимое количество рабочей силы для выполнения задачи. Это приводит к снижению эффективности программы предиктивного технического обслуживания. То есть философия фазы обнаружения заключается в том, чтобы провести как можно быстрее как можно больше обзоров машин.
Фаза коррекции: Фаза коррекции требует замены или ремонта отказавшего компонента и проверки коррекции. Это также идеальное время для устранения причины отказа.
ПРЕДИКТИВНЫЕ ТЕХНИЧЕСКИЕ СРЕДСТВА
Эффективное техническое средство для предиктивного обслуживания должно быть портативным, легким и выполнять повторяемое, неразрушающее тестирование. Существует много различных технологий и приборов, которые могут выполнять этот очень важный процесс. Тем не менее нет ни одного измерения или технологии, которые бы предоставили 100% понимание отказов подшипников с качающимися элементами. Более того, многие из доступных техник очень хорошо справляются с обнаружением отказов подшипников с качающимися элементами, но обладают ограниченной способностью выявлять другие дефекты в машинном оборудовании.
АНАЛИЗ ЭЛЕКТРИЧЕСКИХ ПОДПИСЕЙ
Анализ электрических подписей (ESA) доказывает свою эффективность как инструмент для выявления начальных отказов подшипников с качающимися элементами на самой важной стадии - фазе обнаружения программы предиктивного технического обслуживания. ESA также обладает дополнительной возможностью выявления начальных отказов не только в подшипниках с качающимися элементами, но и в электромоторах, трансмиссиях, помпах, конвейерах и другом машинном оборудовании.
МЕТОДЫ АНАЛИЗА ВИБРАЦИЙ
Методы анализа вибраций широко используются для выявления неисправностей в механическом оборудовании, включая подшипники с качающимися элементами. Этот метод основан на анализе вибрационных сигналов, которые генерируются оборудованием в процессе его работы.
Анализ вибраций позволяет выявлять различные типы неисправностей, такие как дисбаланс, выравнивание, ухудшение смазки, повреждение подшипников и другие. Путем мониторинга вибраций оборудования и анализа полученных данных можно определить степень износа и состояние подшипников.
УЛЬТРАЗВУКОВОЕ ОБНАРУЖЕНИЕ
Ультразвуковое обнаружение также является эффективным методом для выявления неисправностей в подшипниках с качающимися элементами. Этот метод основан на измерении ультразвуковых сигналов, генерируемых дефектами в подшипниках.
Ультразвуковое обнаружение позволяет выявлять ранние признаки дефектов, такие как трещины, износ, отслоение и другие. Этот метод может быть использован в дополнение к другим методам предиктивного обслуживания для более полного мониторинга состояния подшипников.
ЗАКЛЮЧЕНИЕ
Выявление неисправностей в подшипниках с качающимися элементами на ранних стадиях их развития является критически важным для обеспечения надежной работы оборудования и предотвращения катастрофических отказов. Эффективные программы предиктивного технического обслуживания включают разнообразные методы и технологии, такие как анализ вибраций, ультразвуковое обнаружение и анализ электрических подписей, которые позволяют выявлять ранние признаки дефектов и проводить своевременное обслуживание оборудования. Эти методы в сочетании с правильной эксплуатацией и обслуживанием могут продлить срок службы подшипников с качающимися элементами и обеспечить надежную работу вращающегося оборудования.
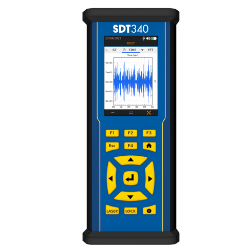
Системы защиты Bently Nevada 3500
Система защиты 3500 от Bently Nevada является широко используемой системой мониторинга и защиты оборудования в различных отраслях промышленности, таких как нефтегазовая, энергетическая, химическая и другие.
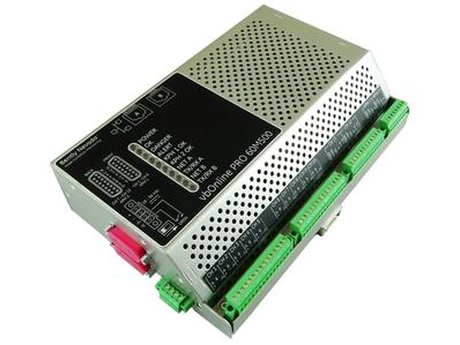
Онлайн-монитор вибрации vbOnline Pro
vbOnline Pro - это онлайн-монитор вибрации, разработанный компанией Bently Nevada. Он предназначен для непрерывного мониторинга вибраций различных типов оборудования, таких как насосы, компрессоры, генераторы, турбины и другие.

Системы защиты Orbit 60
Система защиты Orbit 60 от Bently Nevada - ультрасовременная система мониторинга и защиты промышленного оборудования, предназначенная для обеспечения максимальной надежности и безопасности работы оборудования в различных отраслях промышленности.